Highlights :
- India’s push for battery manufacturing, aims to counter China’s dominance while addressing rising domestic and global energy storage demands
- The need for protection for this sector might risk a rise in energy prices for end consumers yet again, after the protection for solar .
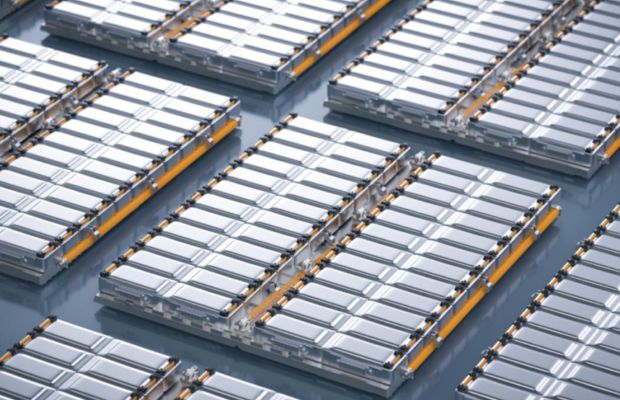
Following the extended trend of protective measures for solar PV manufacturing, and more recently, solar glass, Li-Ion (or LFP ) battery manufacturing could emerge as the next sector to receive similar support from the Indian government. State policies are increasingly being used as a tool to shield domestic industries from the challenges posed by inexpensive and competitive external trade in products and services, especially with China. After all, with energy storage coming to the forefront with higher share of renewable energy, a familiar story is beginning to unfold. Dropping prices, a very high to complete dependence on China, and an infant domestic industry almost certain to be uncompetitive vis a vis Chinese imports.
Indian Battery Manufacturing Scene
Responding to the undeniable need of energy storage systems to solve the challenges posed by the variable nature of renewable energy, India is ramping up its battery manufacturing capacity as well.
While the country’s battery manufacturing capacity is still in its nascent stages, the installed capacity is projected to increase up to 120 GWh by 2027 or 2028 to support the growing adoption of electric vehicles and grid-scale storage in the country. National Electricity Plan (NEP) 2023 of Central Electricity Authority (CEA) states that the energy storage capacity requirement is expected to increase to 411.4 GWh (175.18 GWh from PSP and 236.22 GWh from BESS) by year 2031-32. Keep in mind that PSP storage will be far more susceptible to delays, and you probably have an even tougher ask from battery storage. Which will need to match domestic expectations of low prices.
To reach this enormous capacity demand in the future, Indian players, like Reliance Industries, JSW Group, Amara Raja, and Ola Electric Mobility, are set to add an additional 246 GWh of nameplate manufacturing capacity through to 2035. Many though the PLI scheme for battery manufacturing from the government.
Chinese Challenge
Indian manufacturers are facing intense competition from low-cost Chinese imports, driven by China’s efficient production processes and significantly lower logistics costs for transporting batteries to India. Furthermore, China boasts the lowest battery prices globally. The most recent 16 GWh PowerChina tender is reported to have attracted 76 bidders, with 60 of them below USD 68.4/kWh (INR 5,800/kWh), for a full SYSTEM cost. At a time when equivalent prices in smaller Indian projects are still at over USD 200 (INR 17,000).
Over the past two years, battery manufacturers have significantly scaled up production capacity to prepare for the expected rise in demand from the electric vehicle (EV) and stationary storage markets. Globally, the total battery-cell manufacturing capacity has reached 3.1 terawatt-hours, exceeding the estimated annual lithium-ion battery demand for 2024 by more than 2.5 times, as reported by BNEF. This oversupply has played a role in driving down battery prices.
Battery prices saw their steepest annual drop since 2017 this year, with China leading the trend as average battery pack prices fell to USD 94/kWh (INR 7,981/kWh), the lowest globally. Meanwhile, global lithium-ion battery pack prices declined by 20 percent from 2023, hitting a record low of USD 115/kWh (INR 9,765/kWh). This underscores the resilience and advancement of the Chinese market compared to its major competitors, Europe and the US, where battery pack prices were higher by 31 percent and 48 percent, respectively.
For Indian domestic battery manufacturers, this is posing a stiff competition to grow and survive. Enter the Indian government .
State Policies to Change the Game
India is rapidly positioning itself as a competitive hub for lithium-ion battery manufacturing, with a strong focus on lithium iron phosphate (LFP) cells. As per the Central Electricity Authority (CEA) estimates, India would require 41.7 GW of BESS and 18.9 GW of PSPs by 2029-30. IEA estimates that India is expected to become the world’s third largest market for utility-scale batteries by 2030. State policies will be crucial in achieving this.
To help reduce the input costs for manufacturing lithium-ion batteries in the country, basic customs duty on critical minerals like Cobalt and Lithium, critical for Electric Vehicle (EV) batteries, have been fully exempted in the Union Budget presented on July 23.
India’s Production-Linked Incentive (PLI) scheme for Advanced Chemistry Cells (ACC), launched in 2021 with a budgetary outlay of INR 18,100 crore, forms the backbone of the country’s battery manufacturing strategy. The scheme was launched offering subsidies to manufacturers who meet stringent criteria, including achieving 60 percent domestic value addition within five years and committing a minimum investment of INR 225 crore/GWh of capacity. The scheme envisages to establish a cumulative ACC battery manufacturing capacity of 50 GWh.
These initiatives, combined with lower production costs and import tariffs, create a significant cost advantage for Indian-made LFP cells. With PLI support, these cells should be much cheaper than those produced in China, enhancing India’s global competitiveness in battery manufacturing.
…may result in rising project costs
Measures like hiking import rates to support domestic manufacturers and countering the low prices and growing dominance of Chinese players in the Indian market will increase cost for battery and energy storage projects in India.
Further, this can cause RE project costs to soar, slowing down the renewable energy growth for a brief period. Keep in mind that higher solar module costs in 2024 have been tempered so far by the sharp drop in storage costs, allowing many of the strorage, RTC and FDRE tenders to remain competitive. IF solar prices remain constant (and they could move up in 2025-26) and storage costs also arrest their fall and start moving up, then we have a recipe for resistance from discoms to buy such power. As it is, SECI still have over 9 GW of unsold projects despite attractive prices.
The share of energy storage in renewable energy projects in India is steadily increasing. SBI CAPS projects a 12-fold rise in India’s energy storage capacity, reaching approximately 60 GW by FY32. This growth reflects changes in renewable energy tenders and a notable rise in projects integrating storage solutions, from 5 percent in FY20 to 23 percent in FY24.
Localising Supply Chains is the Key
The state support may help the domestic battery manufacturing industry to flourish in India. The key to achieving this cost efficiency in India will be scaling up production to multi-gigawatt levels and localising the entire supply chain. By localising the supply chain, LFP cells produced in India can become competitive to those manufactured in China, and significantly more affordable than cells made in Germany or the US, both of which exceed cost of Chinese produce. For example, producing a battery cell in the United States is nearly 20 percent more expensive than in China, even when assuming that material costs do not vary regionally.
India’s expanding battery manufacturing capacity offers a dual advantage: meeting domestic demand and tapping into export opportunities in regions like Europe and North America. The open market policies in Europe have favoured Chinese manufacturers, and Indian battery makers could also capitalise on this market by producing a surplus.
However, realising the announced capacity targets depends on addressing several challenges. These include delays in plant commissioning, the maturity of the Indian market, and the limited experience of domestic manufacturers. The country must also be ready for a brief period of difficulties due to rising project costs. Such factors could hinder or delay the achievement of capacity goals. Even China experienced utilisation rates of roughly 40 percent in its lithium-ion manufacturing facilities in 2023. A similar scenario in India could result in supply shortages if local production fails to keep pace with rising demand.